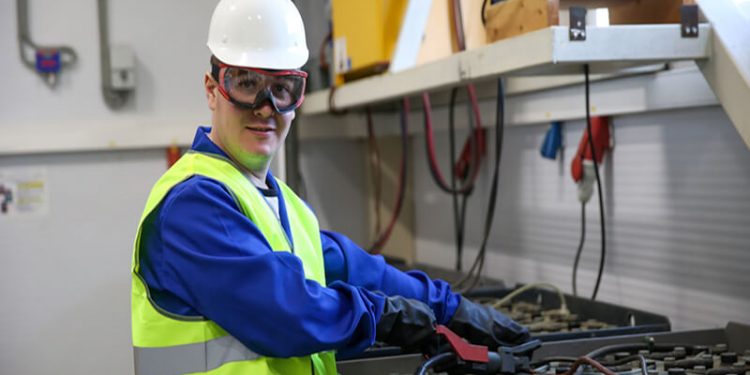
В основе производства современных АКБ лежит принцип максимального исключения человеческого фактора из технологического процесса. На всех этапах изготовления составных частей от приёмки сырья до окончательной сборки стоят автоматизированные комплексы. Каждый из них разработан и изготовлен на специализированном предприятии, поставляться они могут компаниями разных стран, а производитель конечного продукта организует полный цикл и согласование работы участков.
Содержание страницы
Основные этапы производства АКБ
Производство аккумуляторов на современном предприятии широко автоматизировано и разделено на отдельные технологические участки:
- плавка и литьё свинцово-кальциевой ленты из получаемого свинца в брикетах и пакета необходимых легирующих будущие электроды присадочных элементов;
- прокатка ленты и производство рулонов;
- производство свинцовой пасты из порошка;
- формирование пластин на намазочном участке;
- изготовление полипропиленовых корпусов;
- конвертировка электродов и сборка моноблоков;
- пайка групп и отливка токопроводящих мостиков;
- формировка и зарядка;
- контроль качества и отправка на склад готовой продукции.
Технический контроль существует на каждом этапе, поскольку обнаружить производственный брак после окончательной сборки и герметизации батареи уже не получится. Там контролируются лишь электрические параметры.
Создание электродов
Свинец при производстве используется в виде порошка для создания намазочной пасты, формирующей активную зону электродов, а также в слитках (брикетах) для отливки ленты, идущей на создание самих пластин.
Свинцовая паста подвергается контролируемому оксидированию и кристаллизации, чтобы свести к минимуму процессы коррозии в готовом аккумуляторе. Использованы процессы штамповки порошка и перемещения его воздушными потоками, большое внимание уделяется экологичности процесса, свинец – опасный металл.
Электродная лента отливается из свинца и других присадочных металлов в автоматизированной установке, состоящей из печей, прокатных линий и намоточного оборудования. Человек лишь контролирует работу, вся дозировка проводится автоматически. Состав металла контролируется лабораторными методами.
Готовые пластины появляются после формования из ленты и нескольких намазочных операций. В свинцовую пасту добавляются компоненты, обеспечивающие прочность намазки и долгий ресурс. Для удержания её на пластинах и хорошей площади контакта производятся просечные процедуры, химическое и физическое армирование активной зоны.
Сборка и упаковка в корпус
Изготовленные из тепло- и морозостойкого материала корпуса и крышки поступают на сборку, где автоматическая линия подготаливает для них нужное количество пластин по весу и количеству. Электроды конвертируются сепараторами и помещаются в корпуса, после чего проводится отливка и пайка токопроводящих мостиков. Моноблоки завариваются термосварочным роботом.
После очередной проверки качества аккумуляторные батареи подвергаются пропитке электролитом и формированию заряда. Ведётся контроль уровня электролита и его температуры.
Окончательно отмытые, просушенные и заряженные батареи проходят электрические испытания, маркировочные и упаковочные процедуры. Остаётся лишь уложить их на поддоны и отправить на склад.
Внедрение новых технологий изготовления
Отдельные операции по производству различных типов батарей по материалу сепараторов, организации и составу электролита могут существенно различаться, но всё это скрыто в оборудовании участков. Конечный продут – АКБ бюджетных конструкций, AGM-батареи или гелевые источники энергии имеют свою специфику технологий, но общие принципы построения аккумуляторных производств позволяют на одном заводе производить любые товары по мере закупки и внедрения автоматизированных линий на каждом участке.
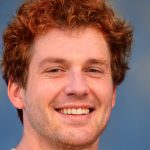
Работал более, чем с 500 компаниями по всему миру. Владелец собственного бизнеса и блога.
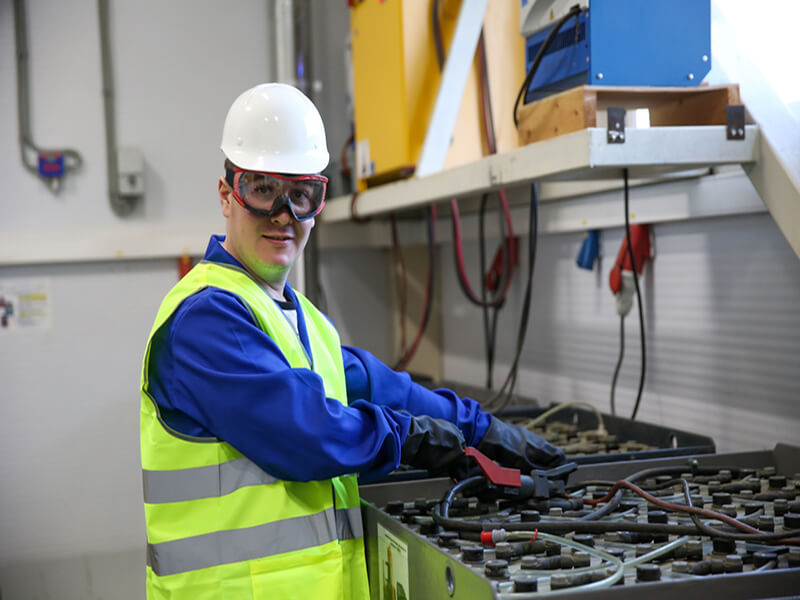